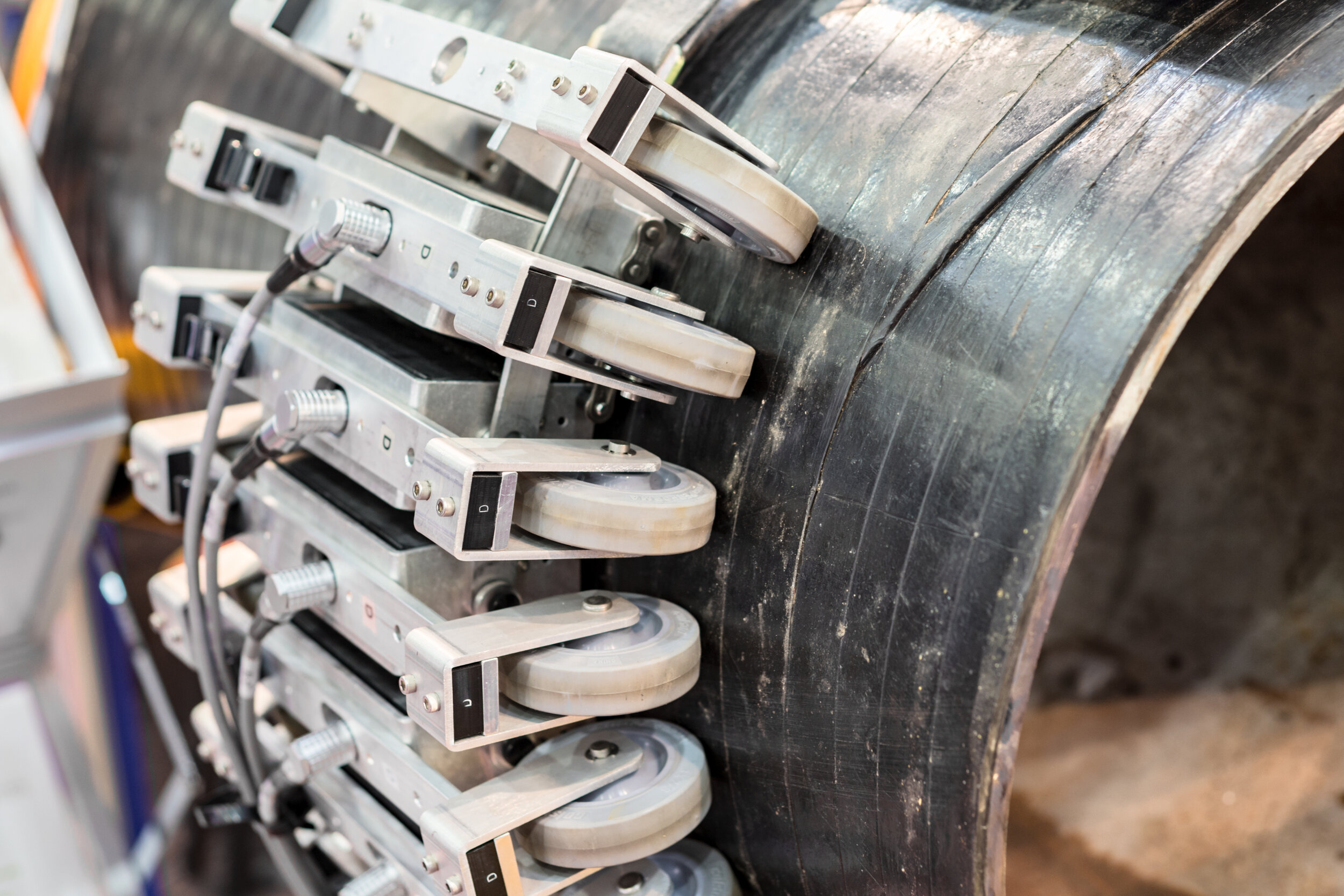
Advanced NDT
Prime Inspections provides certified technicians to execute advanced nondestructive testing services, ensuring unparalleled accuracy, consistency, and depth of analysis for asset damage, including flaws that are undetectable by conventional standards.
Utilizing the latest in inspection technology, our advanced NDT services pinpoint irregularities, analyze their properties, and provide essential data to pipeline and facility managers, enabling informed decisions regarding the maintenance, repair, or replacement of assets that may have sustained damage.
Target Underlying Problems
Weld Inspection and Flaw Detection
Crack Detection and Characterization
Corrosion Detection and Monitoring
Detection of Material Degradation
Inspection of Coatings and Linings
Comprehensive Structural Analysis
Advanced NDT Methods
-
Automated Ultrasonic Testing (AUT)
Automated Ultrasonic Testing (AUT) extends to a wide range of methods used to target damage and/or degradation located externally or internally of the component. Our AUT services capture highly detailed inspection data with great accuracy and repeatability.
-
Phased Array Ultrasonic Testing (PAUT)
Phased Array Ultrasonic Testing (PAUT) detects and images defects, including cracks, voids, and pits caused by corrosion. It also measures material and coating thickness, detects changes in material properties, and maps adhesive. Common applications include assessing the quality of welds and rivets and inspecting joints and interfaces.
-
Time-of-Flight Diffraction (TOFD)
Like most UT methods, Time-Of-Flight Diffraction (TOFD) works by emitting sound waves into a component and measuring the response time of low-amplitude waves diffracted by the tips of cracks. TOFD is one of the fastest NDT methods because it only requires one scan to find any defect information within the weld. It can locate and measure the size of many different types of defects with incredible precision.
-
Laser Shearography
Commonly used to inspect large, complex components, Laser Shearography provides surface deformation and strain information in real time. Due to its simple setup, direct strain measurement, and relative insensitivity to environmental interruptions, shearography is considered one of the best NDT methods for inspecting delaminations of relatively thin panels made from composite materials and honeycomb structures.
-
Digital Radiography
Computed Radiography (CR) uses a phosphor imaging plate that replaces film in conventional radiography techniques. First, it indirectly captures the image of a component on a phosphor plate, then converts the image into a digital signal that can be visualized on a computer monitor. Image quality is fair but can be enhanced using appropriate tools and techniques without compromising integrity.
Direct Radiography (DR) uses a flat panel detector to capture an image directly and display it on a computer screen. This technique is fast and produces high-quality images.
Real-Time Radiography (RTR) works by emitting radiation through an object. These rays then interact with a special phosphor screen or flat panel detector containing micro-electronic sensors. The interaction between the panel and the radiation creates a digital image that can be viewed and analyzed in real time.
-
Corrosion Mapping
Corrosion Mapping provides quantitative data on areas where corrosion or erosion has reduced the wall thickness. This technique is also called AUT Corrosion Mapping, C-Scan, or Ultrasonic Corrosion Mapping. It is best known for its ability to quickly identify wall loss and present a detailed analysis of the location, thickness values, and area.
-
3D Laser Mapping
3D Laser Mapping provides significant detail and accuracy in a short timeframe. This method of NDT enables detailed 3D surface images of corrosion underneath the asset's surface. Other visualizations include wall loss data, corrosion dimensions, volumetric loss data, and cross-sectional profiling. The advantage of 3D laser mapping is the potential time savings and productivity.
-
Laser-Induced Breakdown Spectroscopy (LIBS)
Laser-Induced Breakdown Spectroscopy (LIBS) is used to determine the elemental composition of materials. It provides easy, fast chemical analysis with reasonable precision, detection limits, and cost. LIBS measures light elements in low concentrations, such as aluminum, silicon, and carbon. The LIBS analyzer enables users to easily grade H and L-grade stainless steels, low alloys, and carbon steels.
Recent PHMSA safety rules require gas pipeline operators to ensure material records are 100% traceable, verifiable, and complete. Testing for chemical composition is a critical step where records may be incomplete.
-
Positive Material Identification (PMI)
Positive Material Identification (PMI) is the analysis and identification of materials through various nondestructive methods, such as Optical Emission Spectroscopy (OES) and X-ray fluorescence (XRF). OES offers a more complete view than XRF and is the only method that can distinguish between levels of carbon in a material. XRF helps determine the chemical composition of any unknown material. However, it cannot distinguish between material grades in certain elements, such as carbon and silicon, among others.
X-ray Fluorescence (XRF) is one of the most common NDT techniques with fast, reliable results. XRF can measure light elements in low concentrations, such as Magnesium, Aluminum, Sulfur, Phosphorus, and Silicon. However, XRF analyzers cannot measure carbon, so they are incapable of grading carbon steel, low-carbon stainless steels, and low-alloy materials.
Optical Emission Spectroscopy (OES) is a fast method for identifying the elemental composition of various metals and alloys. OES measures carbon and light elements in various matrixes, including nickel, stainless steel, carbon steel, etc. OES is ideal for applications that require knowing the exact quantitative breakdown of a solid material.
-
Ultrasonic Shear Wave (UTSW)
Ultrasonic Shear Wave (UTSW) is ideal for hard-to-access areas such as boilers, nozzles, and full penetration welds. Flaws can be characterized and height-sized using an A-scan signal. The results help inspectors accurately characterize and size anomalies within weldments and pipe bodies.
-
Drone NDT
Drone NDT services use drones equipped with advanced sensors and cameras to inspect infrastructure without causing damage. This method allows for safe, efficient, and accurate assessments of hard-to-reach areas, such as pipelines and industrial structures. The drones collect high-resolution images and data, which are then analyzed to detect potential issues like cracks, corrosion, and other defects. This innovative approach improves safety, reduces inspection time, and lowers costs compared to traditional methods.

Complete Inspection Reports
The most important aspect of any inspection service is the final report provided to the customer.
In general, at the completion of an inspection job, we will supply the customer with a final report that includes the following:
It meets the documentation requirements
All important codes and standards included
Quality and acceptance levels for various NDT findings
Drawings, scans, photos, and other visualized data
Inspection summaries and recommendations